7 Factors That Impact Bearing Lubrication in Electric Motors
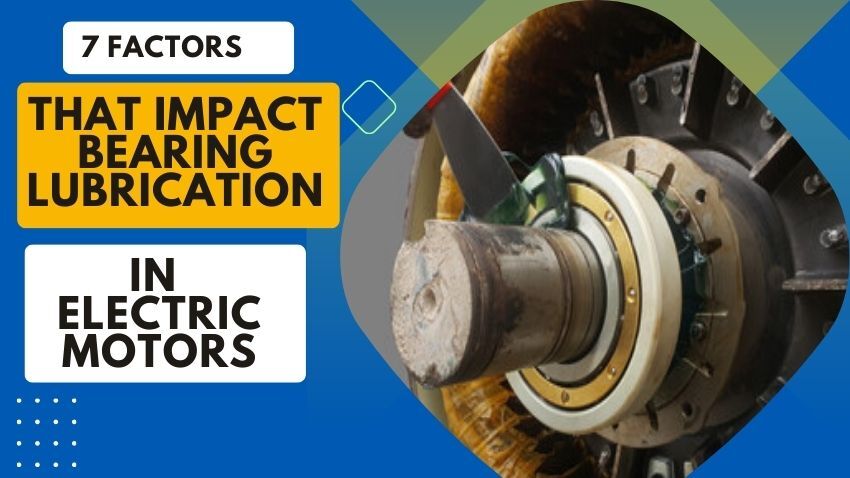
Bearing Lubrication
No matter how you cut it, effective bearing lubrication is crucial for maintaining the smooth operation of your equipment. Several factors impact bearing lubrication in electric motors, including lubricant choice, quantity, contamination control, and proper application techniques.
Adequate lubrication reduces friction, heat, and wear within these bearings, extending their lifespan and preventing premature equipment failure. Regular electric motor repair and maintenance, including proper lubrication practices, are essential to ensure optimal performance, minimize downtime, and maximize equipment longevity.
In this blog, we’ll cover seven factors that can impact the effectiveness of bearings in electric motors and show you some strategies for ensuring your electric motor stands the test of time.
7 Factors That Impact Bearing Lubrication in Electric Motors
If you’ve ever conducted any mechanical or electrical equipment repair, you probably already know just important bearings are. And how crucial proper lubrication is to their longevity. Let’s take a look at seven factors that can impact the effectiveness of your bearings:
1. Operation Time
The duration of motor operation plays a crucial role in bearing lubrication. Motors that run continuously for long periods require more frequent lubrication. On the other hand, motors with intermittent operation may need special lubrication strategies to prevent lubricant degradation and maintain proper lubrication levels.
2. Temperature
Temperature fluctuations can affect the performance and viscosity of lubricants. Electric motors generate heat during operation, and excessive temperatures can cause lubricants to break down, losing effectiveness. Monitoring motor temperature is essential to ensure the lubricant’s stability and prevent thermal degradation.
3. Bearing Size and Type
The size and type of bearings used in electric motors can impact lubrication requirements. Larger bearings may require more lubricant to ensure adequate coverage and protection. Similarly, different bearing types, such as ball bearings or roller bearings, may have specific lubrication requirements. Understanding the specifications of your motor’s bearings is crucial for selecting the right lubrication strategy.
4. Vibrations
Vibrations are inherent in electric motor operation and can affect the distribution and retention of lubricants. Excessive vibrations can cause lubricants to migrate away from critical areas, leading to inadequate lubrication and increased wear. Implementing vibration monitoring and control measures can help ensure proper lubrication throughout the motor’s operation.
5. RPM (Revolutions Per Minute)
The rotational speed of the electric motor, measured in RPM, influences the lubrication requirements. Higher RPM motors create more heat and friction, necessitating adequate lubrication to dissipate heat and reduce wear. Understanding the motor’s RPM rating and selecting lubricants capable of withstanding the associated demands is essential for effective lubrication.
6. Lubricant Type and Viscosity
Choosing the right lubricant and viscosity is crucial for bearing lubrication effectiveness. Different lubricants have varying properties, including temperature resistance, load-carrying capacity, and anti-wear characteristics. Electric motor repair services recommend selecting lubricants specifically designed for electric motor applications, considering factors such as operating temperature, load conditions, and lubricant life.
7. Operating Environment
The operating environment of electric motors can impact lubrication effectiveness. Harsh environments, such as those with high humidity, dust, or chemical contaminants, can accelerate lubricant degradation and compromise bearing performance. Implementing proper contamination control measures, such as seals and filters, is essential to maintain a clean and optimal operating environment.
Strategies for Proper Care of Electric Motor Bearings
Proper care and maintenance of electric motor bearings are vital for ensuring their longevity and optimal performance. By implementing effective strategies, you can prevent premature bearing failure, reduce downtime, and extend the lifespan of your electric motor. Let’s look at a few strategies that can help you take care of your electric motor bearings:
1. Don’t Over Lubricate Your Bearings
One common mistake in bearing lubrication is over-lubrication. Applying excessive grease can lead to several issues, including increased operating temperatures, seal damage, and energy waste. It is essential to follow the manufacturer’s guidelines and use the correct amount of lubricant. Regularly check the bearings and remove excess grease to maintain proper lubrication levels.
2. Automatic Grease Dispensers
To ensure consistent and adequate lubrication, consider installing automatic grease dispensers. These devices deliver a precise amount of grease at regular intervals, eliminating the guesswork associated with manual lubrication. Automatic dispensers provide a controlled and consistent lubrication process, reducing the risk of under or over-lubrication. This strategy is particularly beneficial for electric motors in remote or hard-to-reach locations.
3. Use Appropriate Grease for Lubrication
Choosing the right grease for lubricating electric motor bearings is crucial for their performance and longevity. Consult the motor manufacturer’s guidelines or seek advice from electric motor repair professionals to select the appropriate grease type. Factors to consider include temperature range, load conditions, and compatibility with the motor’s construction materials. Using the recommended grease will ensure optimal lubrication and protection for your bearings.
4. Consult Professionals
When it comes to the care and maintenance of electric motor bearings, seeking the expertise of professionals is invaluable. Electric motor repair and unwinding services can provide comprehensive inspection, maintenance, and repair for your electric motors. They have the knowledge, experience, and specialized tools to identify potential issues, recommend suitable lubrication strategies and address any problems that may arise. Consulting professionals can help you establish a preventive maintenance plan tailored to your specific motor requirements, ensuring the longevity and reliability of your bearings.
Get Help from Experienced Professionals. Call AES International Today!
Protecting your equipment is crucial to the health of your business. And AES International is here to ensure your business is always running smoothly. Whether you require electrical motor repair and unwinding, troubleshooting, or replacement, our technicians are ready to help. We have years of experience handling a wide range of mechanical and electrical repair projects and the resources to help you!
Our licensed technicians adhere to industry standards and best practices, ensuring you always get the highest quality performance from your machines. Make sure to put the livelihood of your business in experienced hands. Call AES at 866-386-1001 and let us help you avoid costly breakdowns and downtime.
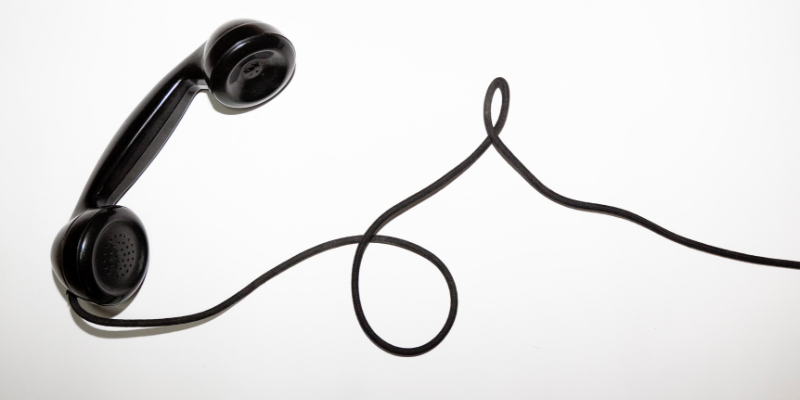
