Everything You Need to Know About CNC Controller Repair
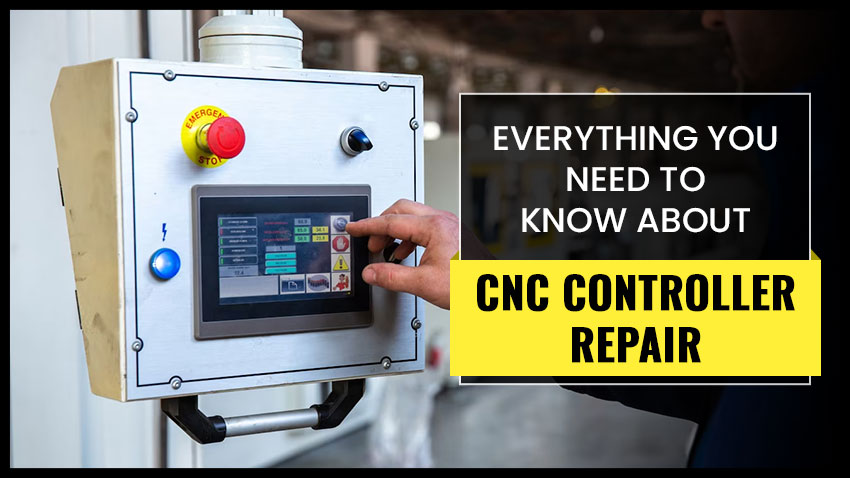
Computer Numerical Control Repair
CNC control systems are vital in modern manufacturing processes, enabling precise and automated control over CNC machines. With their advanced technology and functionality, these systems ensure efficient and accurate production.
However, like any technological system, CNC control systems are prone to malfunction and wear over time. This is where CNC control repair becomes crucial for businesses relying on these machines. When a CNC control system breaks down or experiences glitches, it can bring production to a halt, resulting in significant financial losses. Skilled CNC control repair technicians possess the expertise to diagnose and fix issues, ensuring minimal downtime and maintaining the efficiency of the manufacturing process.
In this blog, we’ll explore everything you need to know about CNC controller repair, including what you need to know to get the most out of your CNC controller without breaking the budget in the process.
Factors That Can Cause Issues with CNC Machines
CNC, or Computer Numerical Control machines, have revolutionized the manufacturing industry, providing precise and automated operations. However, these sophisticated systems are not immune to problems that can disrupt production and impact efficiency. In this blog section, we will explore some common factors that can cause issues with CNC machines, emphasizing the importance of timely maintenance and professional repair services like old CNC control repair or CNC controller repair services.
1. Poor or Improper Maintenance
One of the primary reasons for CNC machine issues is inadequate maintenance. Over time, dirt, debris, and coolant can accumulate, leading to clogged components and affecting the machine’s performance. Regular cleaning, lubrication, and inspection of CNC machines are essential to prevent breakdowns and ensure optimal functioning.
2. Improper Settings or Tools
Incorrect machine settings and the use of improper tools can have a significant impact on CNC machine performance. This includes factors such as false feed rates, improper tool alignment, and using dull or unsuitable cutting tools. Such issues can result in poor surface finish, excessive wear and tear, and even tool breakage. It is crucial to adhere to the manufacturer’s guidelines and use appropriate settings and tools for each machining operation.
3. Improper Programming
Programming errors can cause severe issues with CNC machines. A small mistake in the code can lead to incorrect tool paths, incorrect dimensions, or collisions between the tool and the workpiece. Thoroughly testing and verifying the CNC programs before running them on the machine is essential to avoid costly errors and potential damage.
4. Overheating
CNC machines generate a significant amount of heat during operation, and excessive heat can adversely affect their components. Overheating can lead to thermal expansion, degraded lubrication, and increased wear on critical parts. Regular monitoring of temperature levels, ensuring proper cooling mechanisms, and using high-quality lubricants are essential to prevent overheating and its associated issues.
5. Operator Training
The proficiency and knowledge of the machine operator play a crucial role in preventing issues with CNC machines. Insufficient training can result in incorrect machine operation, improper tool changes, or incorrect material handling. Investing in comprehensive operator training programs can significantly reduce the likelihood of errors and maximize the machine’s efficiency.
To ensure the smooth and efficient operation of CNC machines, businesses must be aware of the factors that can cause issues and take appropriate measures to address them. Proper maintenance, adherence to recommended settings and tools, accurate programming, monitoring for overheating, and comprehensive operator training are all essential elements in preventing the need for computer numerical control system repair.
Preventative Maintenance for CNC Machines
Implementing a comprehensive preventative maintenance program is crucial to maximizing the longevity and performance of CNC machines. By prioritizing these measures, you can minimize the need for costly repairs and ensure smooth operations. If repairs are necessary, seeking professional services like new CNC control repair can swiftly restore your machine’s functionality.
1. Regular Cleaning
Regular cleaning is the foundation of preventative maintenance for CNC machines. During operation, dirt, chips, and coolant residue can accumulate, hindering performance and potentially damaging delicate components. A thorough cleaning routine involves removing debris from the work area, wiping down surfaces, and using appropriate tools to clean the spindle, tool holders, and guides. Implementing a regular cleaning schedule prevents contamination and ensures optimal machine operation.
2. Lubrication
Proper lubrication is essential for reducing friction, preventing wear, and extending the lifespan of CNC machine components. Lubricants help maintain smooth movement and protect against heat and corrosion. Create a lubrication schedule that includes greasing bearings, oiling slideways and ball screws, and checking the oil levels in the hydraulic system. Adhere to the manufacturer’s guidelines for lubricant types and application methods to maximize the benefits of lubrication.
3. Calibration
Accurate calibration is crucial for maintaining the precision and accuracy of CNC machines. Over time, factors such as thermal expansion and wear can affect the machine’s alignment and measurement accuracy. Regularly calibrating key components like tool probes, encoders, and linear scales ensures the machine performs within specified tolerances. Collaborate with experienced technicians or utilize calibration tools provided by the manufacturer to verify and adjust the machine’s alignment as needed.
Connect with AES Today for All Your CNC Control Repair Service Needs!
AES proudly provides computer numerical control repair services for businesses of all shapes and sizes. With years of experience, we specialize in diagnosing and repairing a wide range of CNC control systems, ensuring minimal downtime and maximum productivity for our clients.
We offer comprehensive CNC control repair services, including troubleshooting, component replacement, and system optimization. Whether addressing hardware issues, software glitches, or complex electrical problems, AES has the knowledge and resources to deliver reliable and efficient solutions.
So what are you waiting for? Time is money! Give us a call today at 866-386-1001, and let us ensure your business always operates smoothly.
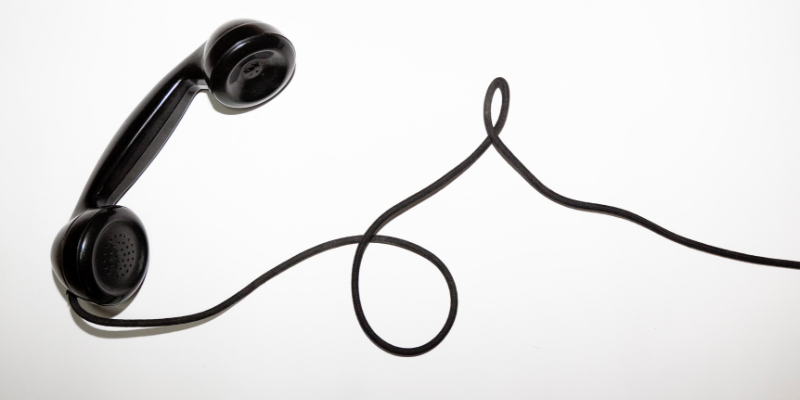
