Diagnosing and Resolving Common Issues with Commercial Power Inverters
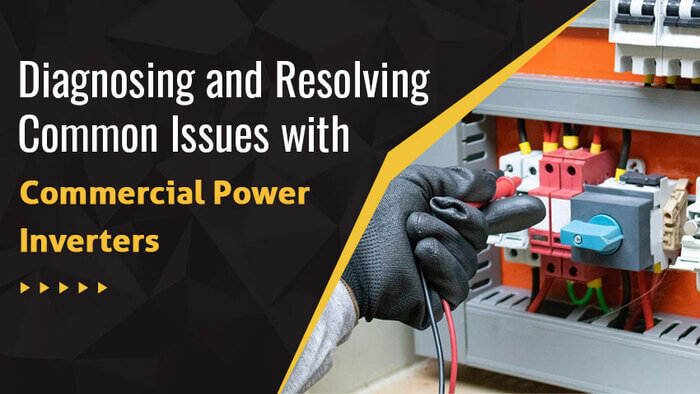
Industrial Power Inverters
A commercial power inverter is a device that changes electrical currents from direct current, or DC, to alternating currents (AC) and is often used in homes, RVs, electronic equipment, and commercial-grade machinery. And, unfortunately, like many important components, there is always the potential for failure.
If you’re faced with a faulty power inverter, you’ll likely need to make quick repairs to minimize downtime and reduce any further risks to your equipment. You can perform power inverter repair on your own If you’re knowledgeable enough about the subject, but in many cases, it’s preferable to seek a professional touch.
In this blog, we’ll explore common issues with commercial power inverters and some handy power inverter repair techniques and provide you with the knowledge you need to get your equipment up and running in no time.
How Does a Power Inverter Work?
Commercial power inverters are designed to convert DC electricity into AC power at the desired voltage and frequency. This conversion process involves several key components, including semiconductor switches (usually insulated gate bipolar transistors or IGBTs), control circuits, and output filters.
First, the incoming DC power is passed through a rectifier, which converts it into a high-voltage DC current stored in capacitors. Then, this DC voltage is chopped into a series of high-frequency pulses that are then filtered to remove any harmonic interference, producing a clean AC output that matches the required voltage and frequency.
The Three Stages of a Power Inverter
To grasp how power inverters perform this transformation, it’s crucial to understand the three fundamental stages involved in their operation: the Oscillator, Amplifier, and Output Power Transformer. In this blog section, we’ll delve into each of these stages to better understand how power inverters work.
1. Oscillator Stage
The first stage in the operation of a power inverter is the oscillator stage. At its core, an oscillator generates a high-frequency signal or waveform, which serves as the basis for creating an AC output. In power inverters, this waveform typically takes the form of a square wave, modified sine wave, or pure sine wave, depending on the type of inverter and its intended application.
The oscillator generates the initial AC waveform by switching electronic components (such as transistors or MOSFETs) on and off at a rapid pace. This switching action alternates the polarity of the DC input, resulting in the creation of an AC-like signal. The frequency of this waveform can be adjusted to match the desired output frequency, typically 50 or 60 Hertz for standard household appliances.
2. Amplifier Stage
Once the oscillator generates the initial AC waveform, it is then passed to the amplifier stage. In this stage, the AC signal is amplified to reach the desired output voltage level. This is crucial because the voltage produced by the oscillator may not be sufficient to power most electrical devices effectively.
Amplifiers within power inverters use electronic components like transistors to boost the amplitude (voltage) of the AC waveform. By doing so, they ensure that the output voltage matches the required level for the connected devices. The amplification process may also involve filtering to refine the waveform and reduce harmonics or irregularities.
3. Output Power Transformer Stage
The output power transformer stage is the final stage in a power inverter’s operation. In this stage, the amplified AC signal is passed through a transformer responsible for fine-tuning the waveform and delivering the AC power to the connected load or devices.
The output power transformer ensures that the AC output is stable and matches the specified voltage and frequency, making it safe and compatible with various electrical devices. It also provides isolation between the inverter’s input and output, enhancing safety and preventing electrical interference.
Common Power Inverter Issues
Like any electrical equipment, power inverters can experience issues that may disrupt their functionality. In this section, we’ll explore some common power inverter problems and how to resolve them:
1. Faulty Power Switches
One of a power inverter’s most basic yet critical components is its power switch. If this switch becomes faulty or fails to function correctly, it can prevent the inverter from turning on or off. To address this issue, you’ll need to inspect the power switch for physical damage or debris. Cleaning or replacing the switch with a new one can often resolve the problem.
2. Faulty Battery
Power inverters often rely on batteries as their primary DC power source. If the battery becomes damaged, weak, or dead, it can lead to power interruptions or an inability to supply AC power. If the battery is old or not holding a charge, it may need replacement.
3. Loose Connections
Loose electrical connections within the inverter, including wiring, terminals, and connectors, can result in power loss or even damage the device. Inspect all electrical connections, both on the DC and AC sides of the inverter and secure them properly. Tightening loose connections is a straightforward fix for this issue.
4. Reduced Backup Time
Over time, the backup time provided by a power inverter may decrease. This could be due to aging batteries, inadequate battery capacity, or excessive power consumption. For this, you may need to consider upgrading to higher-capacity batteries.
Commercial Inverter Repair Techniques
In addition to the aforementioned fixes, we’ve included a few common ways to troubleshoot faulty industrial power inverters. Let’s take a look at both the issue and the fix:
1. Tripped Inverter
A tripped inverter is a common problem that can occur for various reasons, such as overload, short circuits, or overheating. When the inverter trips, it disrupts the power supply to connected equipment.
Solution: To resolve this issue, check for overload conditions by disconnecting non-essential loads. Next, inspect the inverter for signs of overheating or loose connections. Reset the inverter by following the manufacturer’s instructions and ensuring that it has proper ventilation to prevent overheating.
2. Power Inverter Working in Only Inverter Mode
In some cases, a commercial power inverter may operate exclusively in inverter mode, even when connected to an AC power source. This can prevent it from charging batteries or utilizing external power sources effectively.
Solution: First, check the inverter’s settings to ensure it is configured correctly for your intended operation mode. Verify the input source and output settings. If the issue persists, inspect the input power source, including the wiring and connections, for any faults or disruptions.
3. Power Inverter and False Codes
False error codes or fault notifications can sometimes be displayed on the inverter’s screen, leading to unnecessary alarms and downtime.
Solution: To tackle this issue, consult the inverter’s user manual or manufacturer guidelines to identify the specific error code. In some cases, it may be a transient issue or a misinterpretation of conditions. Clear the code per the manufacturer’s instructions and monitor the inverter’s performance. If false codes persist, consult with a professional for a thorough inspection and diagnosis.
4. Noise Emanating from Power Inverter
Noise, such as humming or buzzing, coming from the power inverter can be disruptive and may indicate underlying problems.
Solution: Begin by checking the inverter’s mounting and securing it to minimize vibrations. Inspect internal components, especially cooling fans, for debris or obstructions. Regular maintenance, such as cleaning and lubricating moving parts, can help reduce noise. If the noise remains a concern, consult a professional for further investigation.
AES is Your All-in-One Solution for Your Commercial Inverter Repair Needs
Whether you need industrial inverter repair, or maintenance for servos, electronics, or hydraulics, AES delivers lasting results that allow you to return to business. We focus on efficient maintenance, prompt service, and competitive pricing that keeps your valuable equipment running at full capacity.
So, if you’re ready to give your electronics and machinery a new life, call AES at 866-386-1001. We’ll be happy to provide you with a free quote and help your electronics, machinery, and hydraulics stay in working order.
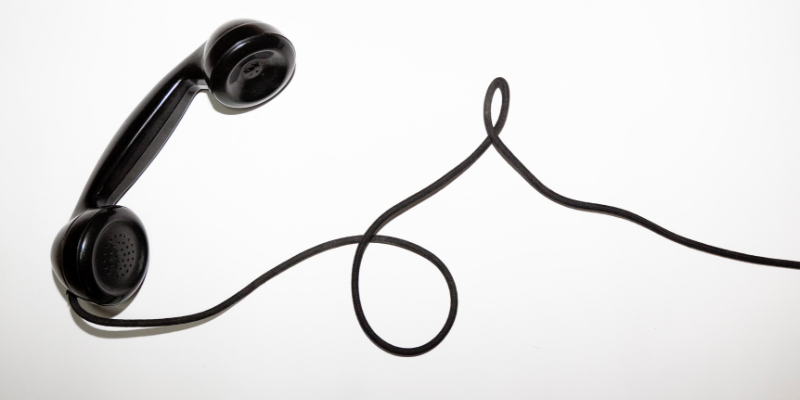
